3D Printing Resin
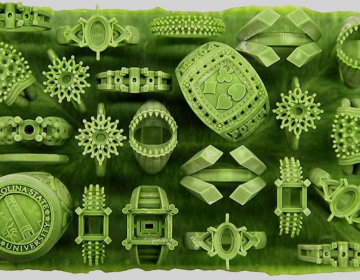
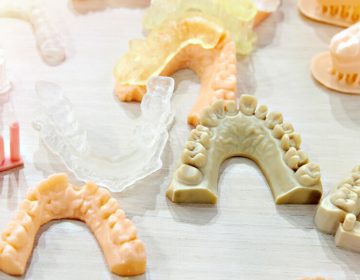
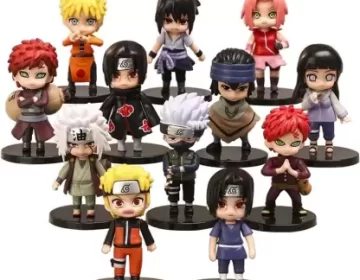
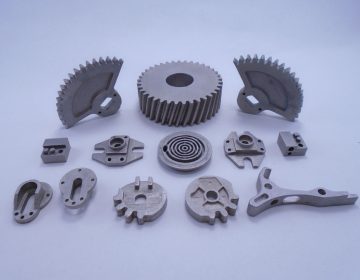
Highlights
- Excellent Choice for Beginners: Standard Colored UV Resin is a top contender for entry-level users. It strikes a perfect balance between printing precision, hardness, and fluidity while integrating seamlessly into the classic formula.
- Unparalleled Precision with Swift Printing: This resin not only guarantees sturdy molded parts with minimal shrinkage but also optimizes print speed, reduces curing time, and maximizes printing efficiency for LCD machines.
- Robust Adhesion, Effortless Detachment: Achieving a high success rate in printing and precision, this resin minimizes the force required to release the model from the forming platform, making shoveling up the model easy. Its low viscosity further simplifies machine and model cleaning.
- Reliable Performance and Broad Compatibility: This resin remains stable and storable across diverse climatic conditions, overcoming the vulnerabilities of other resins susceptible to moisture-induced softening and environmental corrosion. It is attuned to 365-410 nm UV wavelengths and works exceptionally well with Anycubic 3D resin printers.
- Guidelines for Usage: To ensure consistent performance, remember to thoroughly shake the resin before use and keep it tightly sealed and shielded from light post-use. Prioritize safety by wearing gloves to prevent direct skin contact and maintaining proper room ventilation.
Classic Formula for Entry-Level Users
Standard Colored UV Resin stands as the flagship choice among their products, boasting a harmonious blend of attributes that ensures exceptional performance. It excels across a range of critical factors, including printing success rate, adhesion to the print bed, intricate model details, printing precision, hardness, resilience, scent, fluidity, and ease of cleaning. This resin has garnered its best-selling status due to its consistent and well-rounded capabilities, making it a top choice for a variety of 3D printing needs.
General Resin with Balanced Performance
The Colored UV Resin not only meets but surpasses users' expectations when it comes to material performance for general resin. Its exceptional qualities ensure a harmonious balance between stiffness, hardness, resilience, and intricate details. This resin is designed to fulfill a wide range of demands, catering to the diverse needs of users seeking an all-encompassing solution for their 3D printing projects.
Stability and High Model Precision
The molding precision of this resin is consistently maintained within a narrow margin of ±0.2mm. In instances where equipment boasts uniform energy distribution, this precision can be further enhanced to a remarkable ±0.1mm. This refined level of control ensures the production of intricate and distinctive details, contributing to the overall quality and characteristics of the final printed objects.
Smooth Fluidity and Quick Printing
Anycubic's Standard Colored UV Resin displays excellent fluidity, which not only accelerates the printing process but also facilitates quicker molding. This attribute has become even more advantageous with the emergence of monochrome screens, leading to a substantial increase in the molding speed for LCD equipment. The resin's exceptional fluidity contributes to enhanced efficiency in the printing workflow, catering to the demands of modern 3D printing technology.
Various Colors and Wide Applications
A wide array of color options is at your disposal, tailored to cater to your specific requirements. This selection includes not only the most sought-after hues in the market but also pure molding colors that are conveniently paintable during post-processing. This versatile resin finds application in diverse areas, ranging from crafting animation and cultural figure models to creating intricate detailed models, prototypes for appearances, and various structural components. The diverse color choices and adaptable nature of this resin make it a valuable asset across an extensive range of creative and functional applications.
Compatible Mainstream LCD and DLP Printers
Anycubic, a trailblazer in the realm of global desktop LCD 3D printers and desktop DLP 3D printers, has demonstrated a forward-looking approach by factoring in compatibility with both LCD and DLP technologies right from the outset of standard resin's research and development. This foresight ensures that Anycubic's standard resin seamlessly aligns with the prevailing LCD 3D printer and DLP 3D printer technologies, catering to a wide array of users and enhancing versatility within the 3D printing community.
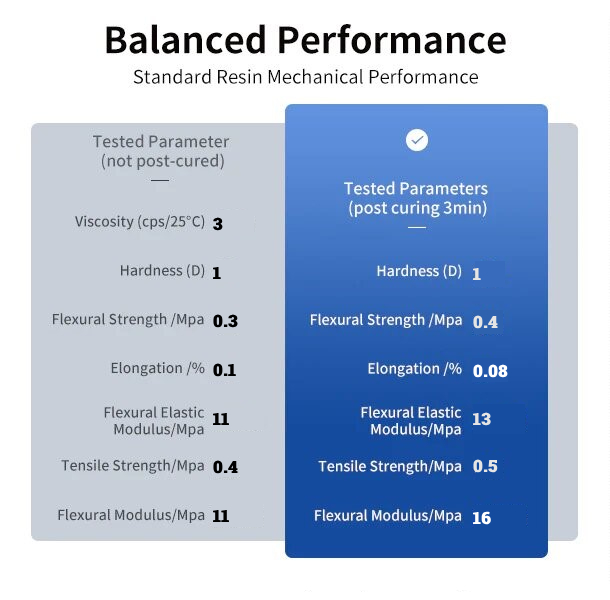
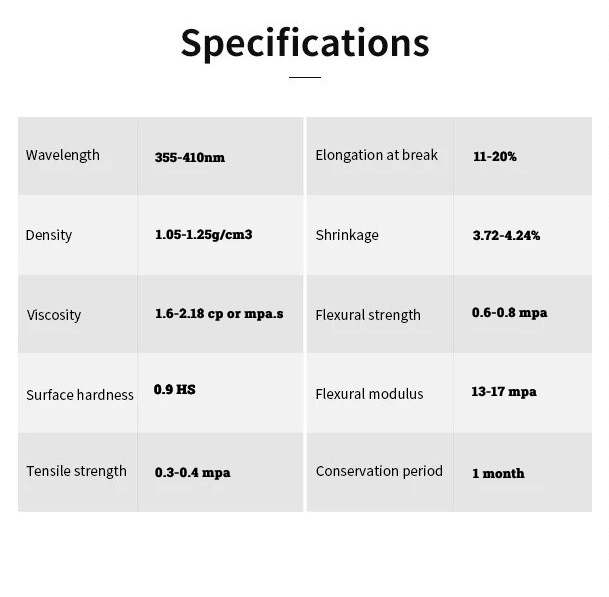
Instructions for Use
⇒ Before use: Shake the liquid resin before use; Clean the resin tank and the molding platform to keep the bottom of the resin tank in light transmission.
⇒ When using: Unscrew the cap and add it to the resin tank according to the equipment requirements; Select the correct print parameters and settings for printing.
⇒ After use: After printing, please use the matching tools for post-processing, including blade, diagonal pliers, tweezers, containers, gloves; ethanol (295%), lactate or isopropyl alcohol cleaning solution.
⇒ Post-processing steps: A. Remove the printed model from the molding platform with a blade; B. Submerge the model in the cleaning solution, rinsed or ultrasonically washed, then taken out and drained; ANYCUBIC Wash and Cure machines are suggested to ensure better effect. C. Proper processing, such as removing support, polishing, coloring, etc.
Precautions
⇒ The ideal condition for storing uncured resin is a cool, dark place at room temperature and protection from light to avoid high temperature or sunlight.
⇒Suggested operating temperature is 18-35°C, and a low temperature may affect the printing effect, thus, the resin can be properly preheated before use (not more than 60°C)
⇒If the resin pigment settles, it can be used after stirring or shaking
⇒ To ensure the performance of the resin, please take out the model in time after cleaning to avoid the model soaking in water for a long time.
⇒ To ensure the mechanical properties of the model, please perform post-curing in time after cleaning and drying.
⇒ To ensure the ideal performance of the curable material, it is necessary to control the intensity and time of the light source after curing. Therefore, the following steps are recommended:
- The intensity of a mercury lamp or LED light source is 5-10mW/m², and the duration is no more than 1 hour (self-regulation).
- The exposure time in the sun (summer) is around 1 hour.
- Proximity or long-term exposure under strong light sources such as high-power high-pressure mercury lamps is prohibited.
- It is recommended to print in a dark room or be covered with a lid while printing as resin is a photosensitive material.